Tools
Tools become great partners in many manufacturing operations. They are the heart of a press, enabling it to cut, bend or otherwise shape sheet metal quickly and with maximum precision. This allows you to create even more complicated mouldings, exactly as you wish. Indulge in consistent quality throughout production and secure the manufacture of millions of products per year with minimal waste.
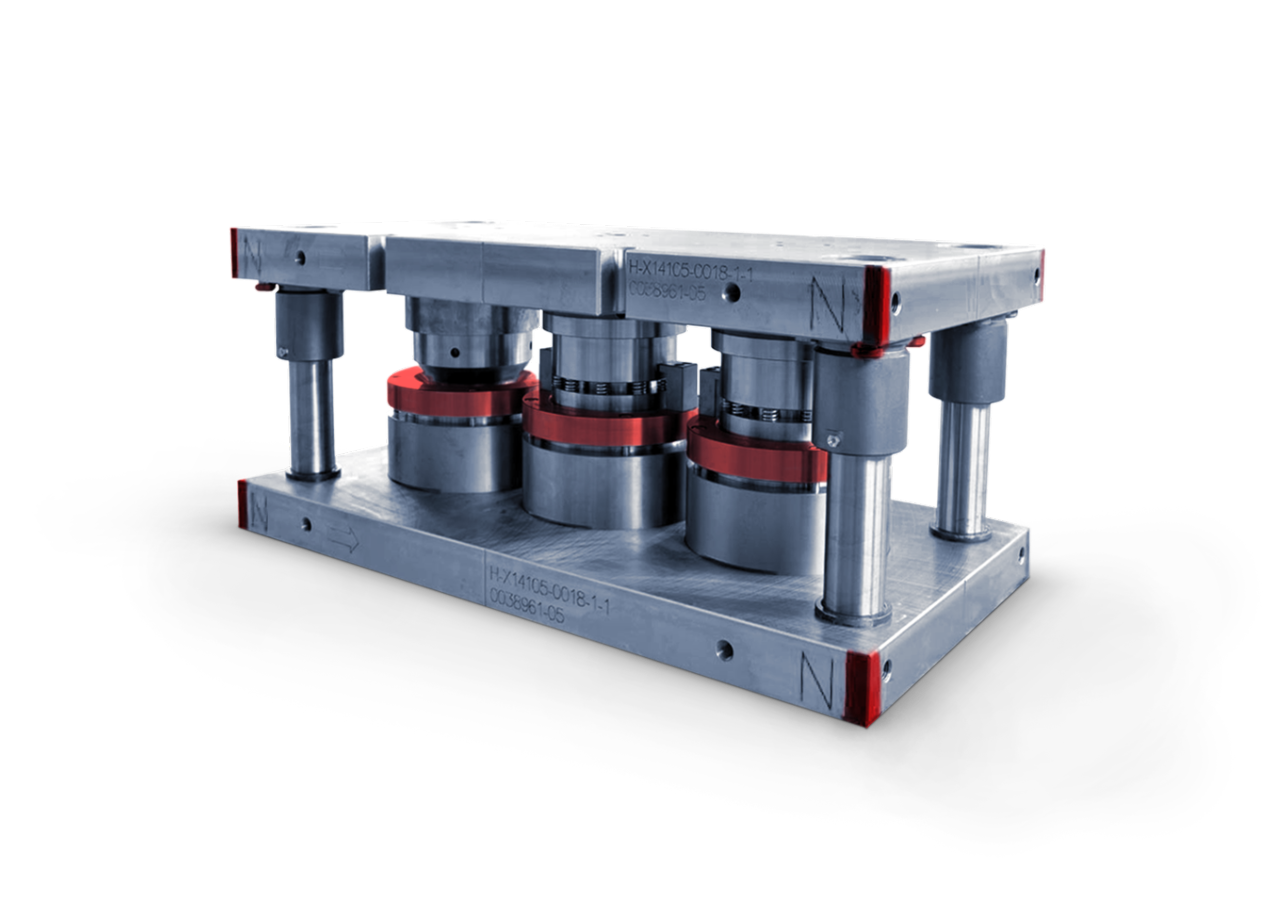
Tools become great partners in many manufacturing operations. They are the heart of a press, enabling it to cut, bend or otherwise shape sheet metal quickly and with maximum precision. This allows you to create even more complicated mouldings, exactly as you wish. Indulge in consistent quality throughout production and secure the manufacture of millions of products per year with minimal waste.
We care about every detail when creating tools. To precisely design them, we use all available technologies, and these technologies are constantly being innovated by us. As a result, you can be sure they will reliably serve you and that the resulting products will also meet the highest standards. In short, we’ll propose a solution that will exceed your expectations. And should you need to change or adapt your production process in the future, we’ll be on hand at any time.
We supply products for many industries
Automotive Industry
Electrical Industry
Construction Industry
Processing Industry
Production Process
Providing the necessary documents
In order to create a tool exactly to your liking, we request all relevant information. We’ll need CAD data and a PDF drawing of the moulding, your internal standards for stamping tools, and information about the specific press and tool clamping. And if you don’t have some of that info available, you certainly don’t have to worry. We’ll do our best to resolve this together to your satisfaction.
Creating a cutting plan
Our seasoned designers will go through all the documents. And because repetition is the mother of wisdom, we’ll re-examine the entire project. Nothing but a 100% result is acceptable for us. We create the final cutting plan and after approval build the entire tool.
Starting production
The drawing documentation travels a few doors down, where experienced technologists take charge. They determine the optimal technological procedure and order the necessary materials. Then they pass the baton to the production staff, who perform a symphony of CNC mills, lathes, and grinders. The conversations fall silent for a while, with only the sounds of cutting, milling, turning, grinding and wire cutting coming from the workshop. Once the noise stops, the parts go to the next station.
Checking everything carefully
Everything is manufactured, and this means that parts are assembled for an inspection measurement by the metrologist. The metrologist thoroughly verifies their quality, and if everything is in order we can go ahead and assemble.
Building a tool
A toolmaker enters the scene and assembles the tool into its final form. The metrologist checks it again as a whole, and the setter then clamps it into the press.
Testing and debugging the tool
At the end of the process, we measure the specific mouldings and, if necessary, tune the tool to perfection. And then there’s nothing to stop it from heading to its new home, where it’ll run like clockwork thanks to careful controls and precision manufacturing.
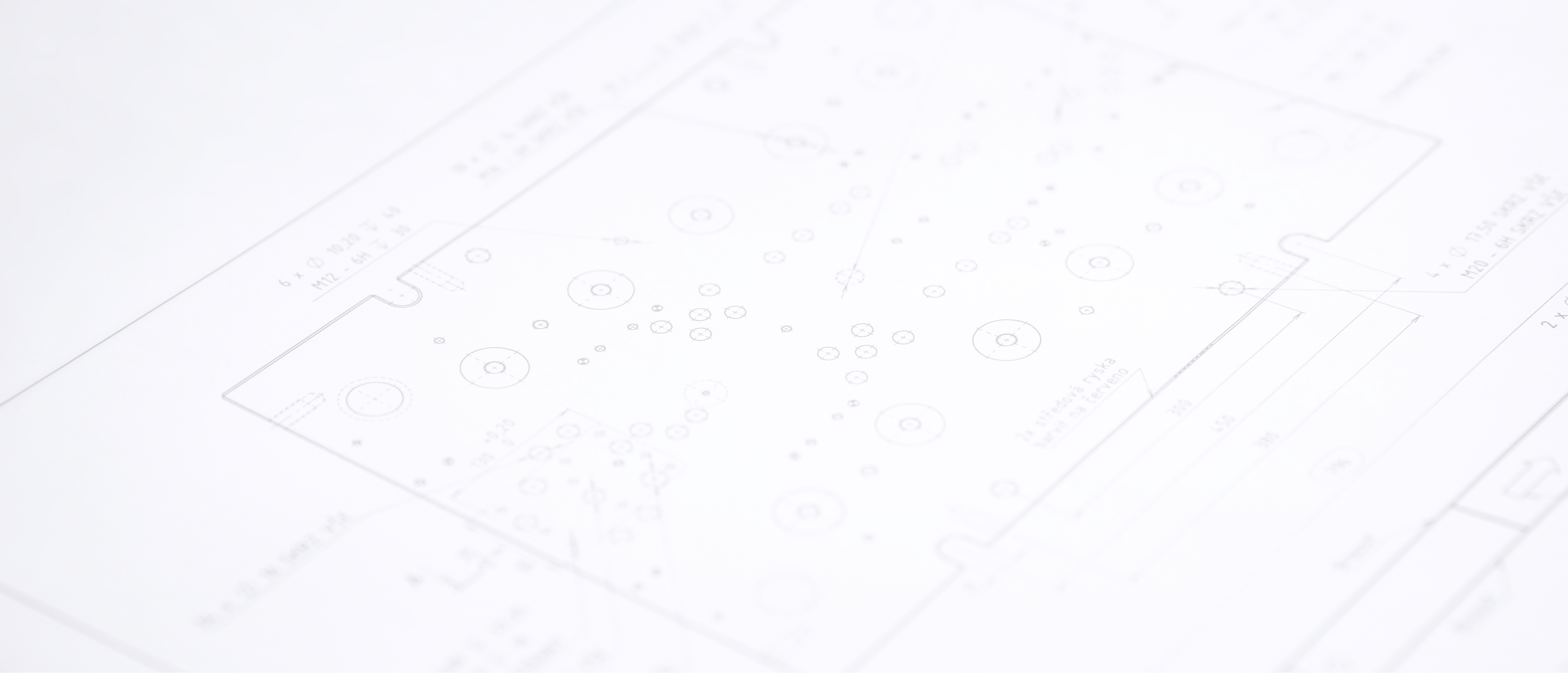
Want to know more?
Do you have any additional questions or do you already know for sure that you need a tool? That’s great news! Just get in touch and we’ll take care of everything else.